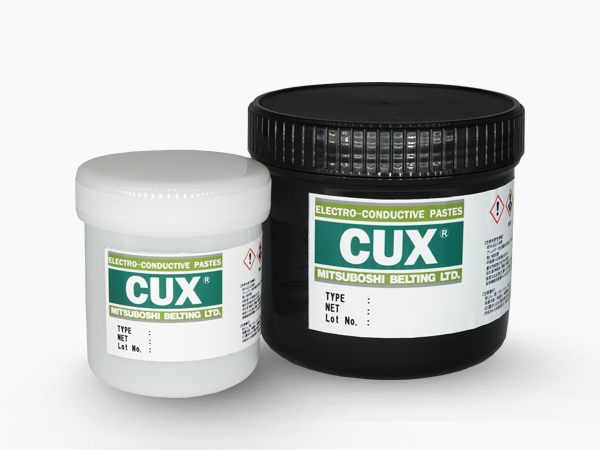
Cu-based
High-temperature Firing Pastes
(1) Al₂O₃ substrate
(2) Copper electrode
(3) CuNi resistive pastes for chip resistor
(4) Overcoat glass
Series | Type | Sheet resistance (mΩ/□ @20μmt) |
Resistance temperature coefficient(ppm/°C) | Viscosity (Pa・s) |
Fired Thickness*²(μm) | Coverage(cm²/g) | Recommended firing condition | |
---|---|---|---|---|---|---|---|---|
HTCR*¹ | CTCR*¹ | |||||||
DH | CNR01DH | 10 | +500±50 | +500±50 | 30~50 | 18~20 | 55 | 900 °C 10min, In N₂ |
CNR03DH | 30 | -100±50 | -80±50 | 30~50 | 18~20 | 55 | 900 °C 10min, In N₂ | |
D | CNR10D | 100 | -90±50 | -70±50 | 30~50 | 20~25 | 68 | 900 °C 10min, In N₂ |
CNR50D | 500 | -60±50 | -30±50 | 30~50 | 20~25 | 76 | 900 °C 10min, In N₂ | |
CN1R5D | 1,500 | -40±50 | -10±50 | 30~50 | 20~25 | 80 | 900 °C 10min, In N₂ | |
CN3R0D | 4,000 | -10±50 | +30±50 | 30~50 | 20~25 | 82 | 900 °C 10min, In N₂ |
Substrate: Al₂O₃, Electrode: Cu, Coating method: Screen printing, Storage condition: Refrigerated
*¹ HTCR:25℃~155℃, CTCR:-55℃~25℃
*² When using standard screen plate, mesh wire diameter: #250-φ30μm, calendar processing, emulsion thickness: 30μm
The resistance value can be adjusted by blending the DH series and D series.
Type | Resistivity(μΩ・cm) | Viscosity(Pa・s) | Fired Thickness*³(μm) | Coverage(cm²/g) | Recommended firing condition |
---|---|---|---|---|---|
DC019(Surface) | ≦ 4 | 75±25 | Ca. 13 | 85 | 900 °C 10min, In N₂ |
DC019U(Back) | ≦ 4 | 75±25 | Ca. 7 | 150 | 900 °C 10min, In N₂ |
Substrate: Al₂O₃, Coating method: Screen printing, Storage condition: Refrigerated
*³ When using standard screen plate
(DC019) Mesh wire diameter: #250-φ30μm, emulsion thickness: 10μm
(DC019U) Mesh wire diameter: #400-φ19μm, emulsion thickness: 10μm
Type | Color | Viscosity (Pa・s) | Fired Thickness*⁴(μm) | Coverage(cm²/g) | Insulator(Ω) | Acid resistance*⁵ | Recommended firing condition |
---|---|---|---|---|---|---|---|
OCG12 | Grayish white transparent | 60±30 | Ca. 13 | 250 | 8.0×10¹¹ | <3.0 | 850-900 °C 10min, In N₂ |
Substrate: Al₂O₃, Coating method: Screen printing, Storage condition: Refrigerated
*⁴ When using standard screen plate, mesh wire diameter: #400-φ19μm, emulsion thickness: 30μm
*⁵ Evaluation method: % weight loss after 1 hour immersion in 0.5wt% sulfuric acid
Please check the Material Safety Data Sheet (SDS) for each product.